A Turbocharged Kawasaki Ninja 250
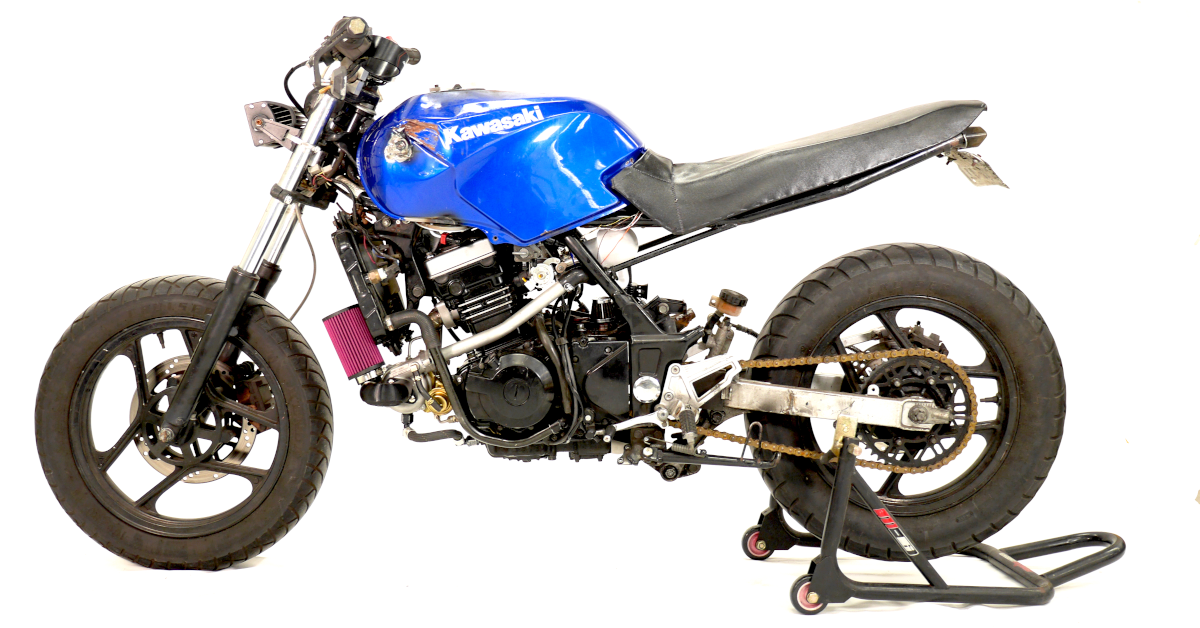
Backstory
This was the first motorcycle I ever purchased, it was used as a college commuter bike. Many, many memories were made on this bike. Unfortunately it had a cracked crankcase from the previous owner. So after a few years of using the bike, the crankcase got swapped out, engine rebuilt and everything else was removed, hidden or tucked. It was ridden for a few more years after that.
Over the years, the idea of turbocharged motorcycles was becoming hard to ignore. The sound, feeling, and power delivery. All of it.
Most turbochargers are fitted on 600+ cc motorcycles, and made well over 250 HP to the wheel! Quite a fast way visit the morgue. Building a slow small displacement turbocharged bike began to look like a good idea.
Goal
The bike is built for only one thing in mind. Pure sensory feedback.
-
0-14,000 RPM.
-
Turbo at 10 psi of boost.
-
6 gears from 0-90 mph.
-
Blowoff sounds in-between.
Horsepower, looks, handling and comfort never mattered.
Pure emotions do.
This idea served as the vision for the build.
The plan
The stars lined up and a 2 week window in my schedule was set aside for the build. Work had to be done quickly and somewhat intelligently to finish the design/fabrication in a timely manner.
That means convert the bike from carburetor to fuel injection AND integrate a turbocharger within 2 weeks.
To pull this off, 2 handy tricks were used.
- OEM fuel injection parts were used whenever possible
- 3D printing was heavily used to increase fabrication speed
If this bike had no sentimental value, it would have been much easier to buy/turbo a Kawasaki Ninja 300/400; a bike with OEM fuel injection. But where's the fun in that? :)
Based on the stock turbo compressor map, the turbocharger should put the bike at 75HP. Just over double of the 33 HP the bike dynoed at.
These power figures are not impressive at face value. But normalized against displacement, the engine will be operating at 300hp per liter with stock compression of 12.9.
Detonation, knock, and mechanical failure are all things to worry about at this power density
ECU Controller
For the budget (500), there are two standalone ECU controllers to pick from.
- Microsquirt
- MicroRusEFI
The Microsquirt ECU is more polished and has widespread support. But ultimately a MicroRusEFI ECU was chosen.
Here are the key reasons why:
- The case/connector layout made much more logical sense on the RusEFI
- Uses an STM32 chip
- Has an open-source repo for both hardware and software that accepts code contributions
The ECU integrates with the following sensors and actuators:
- Throttle Position sensor
- Manifold Air pressure sensor
- Intake air temperature sensor
- Wideband oxygen sensor
- Crank Position Sensor
- Fuel Injector #1/#2
- Ignition Coil #1/#2
- Engine coolant temperature sensor
All of the sensors and mating connectors was sourced from Ninja 300 parts purchased from Ebay. The Ninja 300 harness was spliced out and crimped into the MicroRusEFI ECU.
Intake System
Throttle body
To meet time and cost constraints, an OEM throttle body was used. Thankfully a Kawasaki Ninja 300 has the EXACT same throttle body spacing and bolts right in when using the EX300 intake boots. A little too easy.
For naturally aspirated builds, this section would be done. With turbocharged engines, the air coming out of the turbo needs to be robustly routed into the throttle body, and ideally cooled down via 2 parts.
- Intake plenum
- Charge pipe
Intake plenum
The original plan was to create an sheet metal intake plenum. Making a sheet metal weldment that is fast, cheap, and good. That is hard.
3d printing the part was the only way to meet time, quality and cost. The asynchronous workflow of printing makes it easy to quickly make prototypes, while working on other parts.
All of the critical part interfaces were roughly defined. Throttle body inlet, Charge pipe inlet, intake air temperature sensor and blow off valve position. It was just a matter of connecting the parts with material. The throttle body was measured with a coordinate measuring machine (CMM).
Everything was modeled in Fusion 360, and printed in PETG. 6 revisions was to get everything just right. In hindsight, ridges should have been designed in the throttle body inlet, so T-bolt clamps have something to positively lock against. That will be added in the next revision.
The intake was coated in a clear epoxy for air sealing and a brass threaded insert was installed for the IAT sensor bolt.
Two questions you might have:
- Where is the intercooler?
- Is the 3D printed intake going to fail?
Dude, where is my intercooler?
Cleanly packaging an intercooler in a motorcycle is very difficult. Most solutions involve large amounts of charge pipe being routed throughout the bike. Thankfully horsepower was never the goal for the build, and the best part is no part. An intercooler never made it into the design.
With no intercooler, the intake air temperature will be increased; making preignition and detonation likely. During tuning process, more effort will be spent on monitoring and being conservative with timing
The idea of doing a super slick 3d printed aluminum plenum with an integrated air to air intercooler was entertained. But the design/build of an aluminum 3d printed heat exchanger plenum PLUS the rest of the build is short of impossible. That project is going to be saved for Stage 2 of this bike.
Will the 3d printed intake fail?
The short answer is that I don't know. The long answer is probably and its okay if it does. The failure mode is gentle, and there is an easy Plan B for when it does. Plan B is 3d printing it out of PEEK or aluminum.
Performing a FEM simulation of this part is completely off the table, due to the lack of material property data, the complex load cases, and the anisotropic nature of 3d printed parts. Can it be done? Yes, with enough time and money. For this exact use case, it's cheaper and faster to iterate physically.
Charge pipe
This is a simple part. Waterjet a flange, bend aluminum pipe. Weld one side of the pipe to the flange, and flare the other side of the pipe. I was running out of time, and didn't machine an O-ring groove in the flange. To seal this interface, flat gasket paper was used.
Not ideal, but it works. Good enough and done is better than perfect and never finished. Worst case, the part gets scrapped, and refabricated in the future.
Fueling System
Adding a turbocharger to an OEM naturally aspirated engine can quickly overwhelm the original fuel system. A triple threat working against your fuel system.
- More horsepower equals more fuel. OEM injectors are normally sized to the designed power output of the car.
- As a turbocharger builds boost, the pressure differential across the injector is reduced. If the fuel pump outputs at a constant pressure and your boost pressure increases, your max fuel flow rate is reduced.
- Most turbocharged engines respond well with E85 fuel. It provides evaporative cooling to the intake charge and increases the octane to 105. The stoichiometric ratio is 12.5 vs gasolines 14.7; This would require an injector sized about 15% larger.
Fuel pump
Many OEM fuel injected motorcycles have an internal fuel pump. It saves space, cools the pump, and reduces noise.
But most EFI motorcycle conversions use an external fuel pump.Taking up valuable space but making it easy to integrate into a gravity-fed fuel tank.
In order to cleanly package the pump a OEM Kawasaki Ninja 400 fuel pump directly into the existing fuel tank. Finding a suitable location to add a large bulkhead was the most difficult part, ultimately it was located just in front of the rider's left knee.
The OEM fuel pump bolt hole positions were measured with a CMM, and the respective o'ring gland was spec'd according to parameters in the Parker O-ring handbook. The prototype flange were printed first, then the real part was made from mild steel via CNC waterjet and 3 axis CNC mill.This created the new weldment and was welded into the OEM tank.
Sheet metal was rolled and welded to the inner diameter of the flange. The actual act of notching the OEM tank was tedious and very ARSTENIAL. Not exactly my cup of tea. A dremel with a 1/8" end mill made the cuts in the fuel tank. After TIG welding everything, the entire assembly was pressure-tested for leaks. It passed with flying colors.
In retrospect, the fuel tank could have been 3d scanned and a cut jig designed/printed, but time was getting tight.
SAFETY NOTE: Pleasing use EXTREME caution when welding fuel tanks. You can kill yourself, if trace amounts of fuel are present.
According to the factory service manual, the fuel pump operates at 43 PSI, and has an internal fuel pressure regulator that has no boost reference. Proper turbo installations would use an aftermarket fuel pressure regulator that has a boost reference feature. For this build, it adds time and cost, the two things I don't have time or money for.
Fuel injectors
At 10 psi of boost, the pressure differential across the fuel injector will be 33 PSI, a whooping 23% reduction! The OEM EX300 injector will be a bottleneck at tune time. Using stock EX300 injector was one less thing to worry about during design/fab time. Once the bike has a rough tune, larger injectors will be installed.
The current plan is to spec out an injector that is large enough to flow fuel at the worst case conditions. 33PSI fuel pressure, 10 PSI boost, E85 Fuel. Free lunches don't exist, using a very large injector will reduce idle quality and low rpm-low load lambda control. A trade off that is okay for this project.
Is it possible to spec injectors that work across a HUGE fuel flow rate range? Yes. If you boost reference your fuel pressure regulator and use high quality injectors (ie. Injector Dynamics/Bosch EV14 brand), it will take you a long way. When that solution doesn't scale to high enough fuel rates, stage injection can be used.
Staged injection is when two injectors are installed per cylinder. One injector is smaller and very suitable for idle/low-load, and the other injector is used for high rpm/boost/load conditions. The handoff between small/large injector is fixed in software. Pretty neat!
Turbo System
If a smaller turbo existed, it would have been used. Not many turbos exist at such a low power level, subsequently not much thought was spent analyzing the compressor map for the application.
The turbocharger selected is a VZ21 Ebay turbo. A clone of the RHB31 turbo. It's a liquid cooled, journal bearing turbo that fits in the size of your hand. Based on a compressor map found online, the turbo will produce about 75HP worth of airflow.
This had a couple of features that made it tougher to integrate:
- Integrated Wastegate
- Watercooling capabilities
The integrated wastegate allows the overall packaging to be much tighter with reduced part count. A big win. A direct consequence is that a custom turbo exhaust outlet had to be created. All those details are covered in the exhaust section.
Plumbing in the watercooling lines is overkill based on how the bike is going to be used, but I'm a sucker for stainless hardlines, and slick packaging.
Turbo Intake
Running unfiltered air into your turbo/engine is usually a bad idea. An adapter had to be designed that allows an air filter to be attached to the turbo.
A generic small air filter was purchased on Ebay and drove the packaging of the filter adapter. The perfect air filter would have been the size of a pringle can.
Similar to the intake plenum the air filter adapter is 3d printed. If the part fails due to heat, the failure mode is gentle, and the new part will be printed out of PEEK.
Exhaust System
Most bespoke fabricators/welders can be considered modern day artisans; with years of experience in the craft, an eye for design, and great intuition with an angle grinder.
I have almost none of that. I can TIG weld, and use a computer. My freeform angle grinder skills are closer to a 10 year old child than a full grown adult.
From my experience it is easier to tell a computer what you want, and then have the machines do the tedious work for you.
Here is the general workflow for CAD/3d-print enabled fabricated weldments:
- Prototype the parts in CAD, 3D print the result, and check fitment in real life. Repeat until you are happy.
- Use CNC machines to create the actual part and associated tooling.
- Manually TIG weld the part with first time quality.
Pre-turbo exhaust manifold
Packaging drove the entire design of the manifold, and zero thought was given to exhaust runner lengths. The turbo needed to be mounted as high as possible to accommodate the oil drain line.
It took about 3 revisions to place the turbo in the highest and closest position to the engine case.
The production part needed to be a stainless steel part. 3D printing it out of stainless was out of the question for cost and time reasons.
A 3D printed fixture can be used to hold the stainless parts in the correct position while tack welding. This is fast and high accuracy. A little bit of CAD creativity later, a 3d printable weld fixture with integrated band saw cut jigs was created.
Now it was a matter of manually cutting stainless pie cuts on a chop saw, dropping it into the jig, and tack welding it. Nice and easy.
Post turbo exhaust dump pipe
The hot-side turbo outlet had odd geometry which made simple fabrication techniques out of the question.Similar to the exhaust manifold; it was simply a process of CAD, print prototypes, CNC cut the parts.
The final design isn't conducive to reducing head loss coming out of the waste gate, but that's ok. It is fast and easy to build.
The workflow for this part was similar to the previously mentioned parts.
- Measure the part (CMM)
- Design on computer (CAD)
- Check fit with plastic prototype (FDM printer)
- Make real part (CNC waterjet + TIG welder)
After CNC water jetting the parts out of stainless, it was just a matter of TIG welding it together.
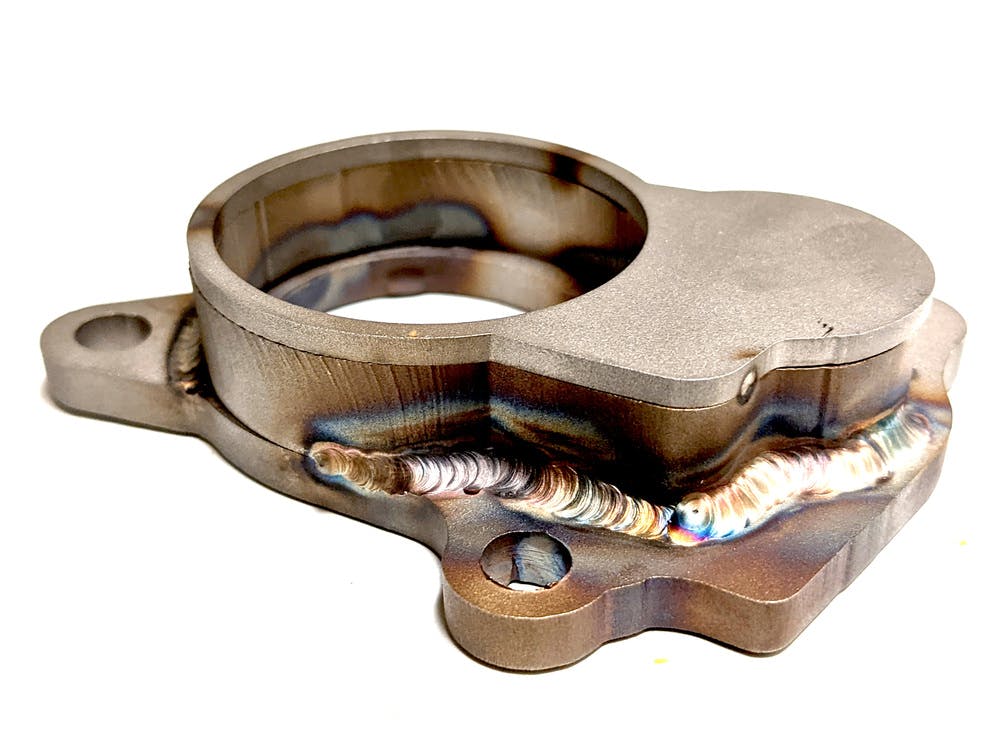
The wideband oxygen sensor was installed in front of the lower engine case, making the sensor almost invisible.
Oiling System
All turbochargers required an oil feed and drain line.
The oil feed was cleanly accomplished by adding to the banjo bolt stack on the left side of the motor.
All stainless steel hardline and tube nuts were used due to the relatively close proximity to the exhaust headers.
The drain line was the most difficult decision of the entire build. The original plan for the drain was to have it drain into the crankcase through the oil fill spout, but it wasn't possible to mount the turbo high enough.
An electric scavenging pump could have been added to pump the oil back into the crankcase, but that solution adds more parts and complexity to the build.
TIG welding a -8 AN bung directly in the lower engine case was the only obvious solution. The end result isn't pretty, but neither is welding cast aluminum.
Coolant System
Watercooling the turbo could have been completely optional, but the turbocharger already had provisions for it.
On the Ninja 250, a conveniently located coolant pipe was modified with -4 AN fittings in order to accept the inlet/outlet ports of the turbo.
The EX300 water temperature sensor threaded perfectly into the EX250 thermostat housing, but the sensor head is too long and would interfere with the thermostat operation. A simple bung extender needed to be machined. This was all done on a manual mill and lathe.
Calibration and Tuning
Not done yet. :) Sign up at the bottom to get updates from me.
Cost Breakdown
The overall cost to add fuel injection and turbocharge the bike was about $1300 dollars. See below for the specifics.
Item | Price (USD) |
---|---|
RusEFI MicroRusEFI | $373.43 |
LC2 Wideband controller + sensor | $170.26 |
VZ21 Mini Turbocharger | $131.60 |
2014 EX300 Throttle body + Fuel injectors | $84.99 |
Dyno Tune | $80.00 |
Banjo and AN Fittings | $68.61 |
2018 EX400 Fuel pump assembly | $66.66 |
Stainless fasteners for final assembly | $42.15 |
Wire splices, ampseal cap, plugs | $37.71 |
Epoxy for coating intake | $28.32 |
2015 EX300 Igntion coils | $24.95 |
2014 EX300 Wire harness | $21.60 |
25MM Ebay Blowoff valve | $21.35 |
Aftermarket Bosch ignitor | $19.03 |
2014 EX300 Intake boots | $14.83 |
Crimps and connector ignitor module | $13.47 |
EX300 2013 Air temp sensor | $9.99 |
Vaccum Line .2" ID | $7.27 |
AN -4 90 Degree fitting | $6.15 |
Total | $1,240.32 |
Preformance Results
The bike was dynoed at 33 HP as a NA carburated bike. Once the bike is tuned, it will be dynoed and the results will be posted here.
Current Status
Getting the ECU tuned. (Written September 2022)
Did you enjoy this website?
Operating at the intersection of mechanical, software and electrical engineering is wildly interesting for me.
These projects can take months to complete, and I'd love to email you when I post new content.
Similar to other personal websites. I will never spam or distribute your email.